Safety in a warehouse is something employers should take very seriously. Workers are at a high risk of injury should the premises lack maintenance and this often means a very large probability of company loss- in reputation, staff and profits- at the end of the day. Here are some of the best practices you need to adopt if you want to maximize warehouse safety:
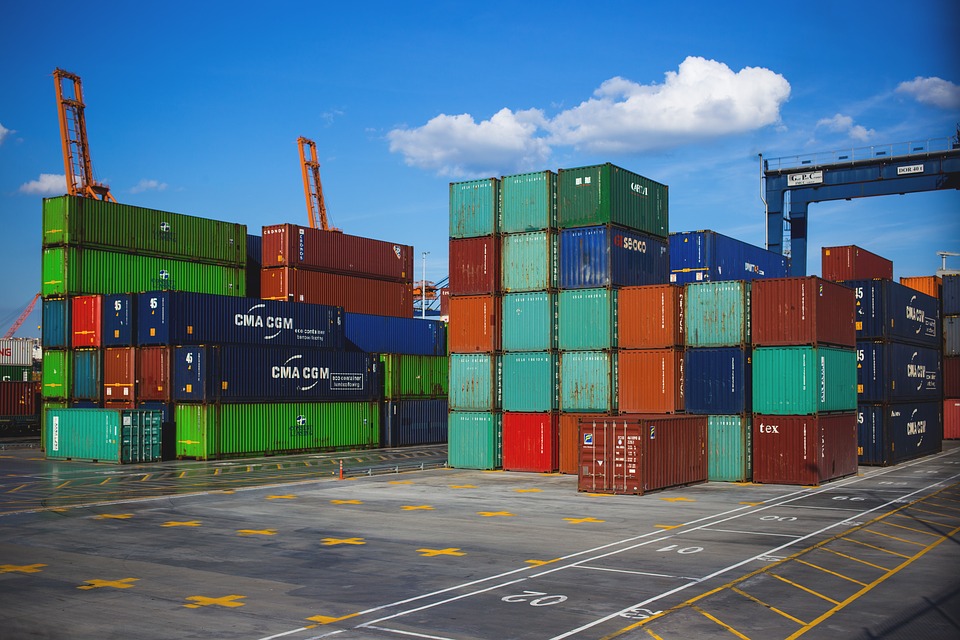
Regular Training
Whenever there’s a speedy change to safety precautions, just informing your employees that the safety manual has been updated won’t do the trick. You need to schedule a training session with each update and make sure both your new employees and old are up to speed with all the new practices. This applies to any change in kits, new equipment and also includes any information regarding on-site machinery. Word of mouth won’t cut it and neither will handing out a new manual. The best way to instill good practices in your employees is by doing it face-to-face.
Cleanliness
Slips and falls are the most common way to obtain an injury in this line of work. Spills are incredibly common, which is why cleanliness is of the utmost importance. To reduce this, make sure there is a team on standby, rotated on a shift basis just to ensure that the floors are clear and spill-free. Make sure these employees have their spill kits on hand to clean up the mess immediately. Ideally, trash bins should be regularly cleared out and daily inspections should be carried out consistently by shift managers.
Signage
Every warehouse needs sturdy safety barriers (check out waresafety.com.au for more). However, as a responsible employer you also need to invest in the proper signage to communicate to your employees where they might encounter hazardous/flammable materials, where there is a fall risk etc. Visual cues are always better than having to rely on word of mouth communication because warehouses tend to be quite noisy and chaotic. While veterans in the field would be more aware of the risks and the lay of the land, newbies might fall prey to avoidable accidents.
Open Forum
The employees get as much a say in devising safety practices as much as you do. In fact, they might even be able to produce some good insight from practical experience that you might have missed in your rounds. While being a firm boss is important, being humble can also be quite productive. If any accidents do occur in the workplace, make sure to bring them up during a meeting and discuss some preventive measures that might come in handy.
Monitor Equipment
Your product inventory isn’t the only thing you need to monitor with a beady eye. Consistently monitor your equipment- make sure all the extinguishers are working and make sure all employees have well-fitting belts. Routine checks are one of the best ways to prevent potential accidents from becoming a tragic reality.
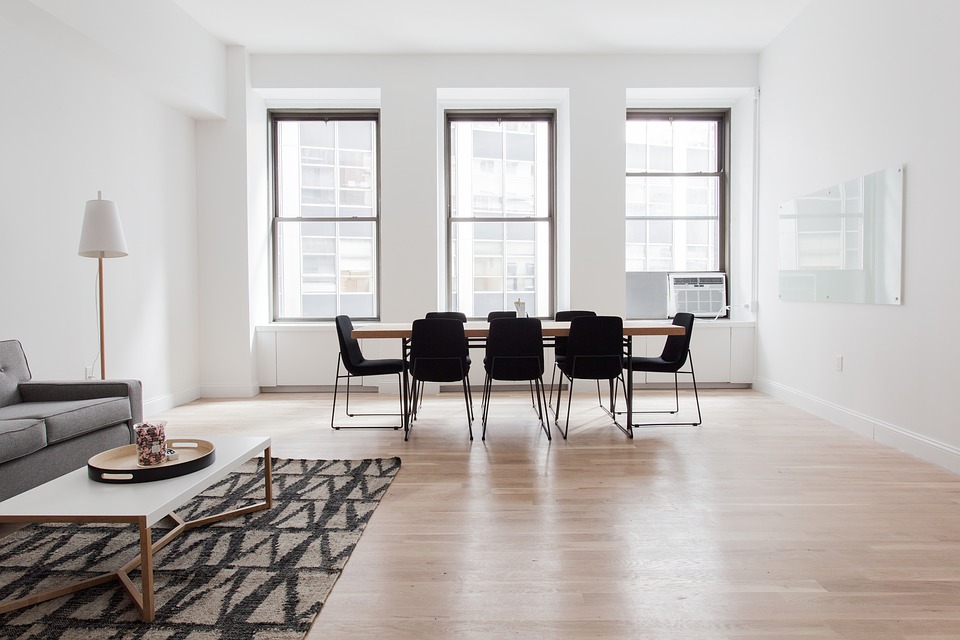
These are the best methods you can use to ensure the safety of your workers. Remember, this is your number one priority and determines your success as a company so it is definitely worth investing in.